Exploring the Benefits of Aluminum Busbars in Electrical Systems
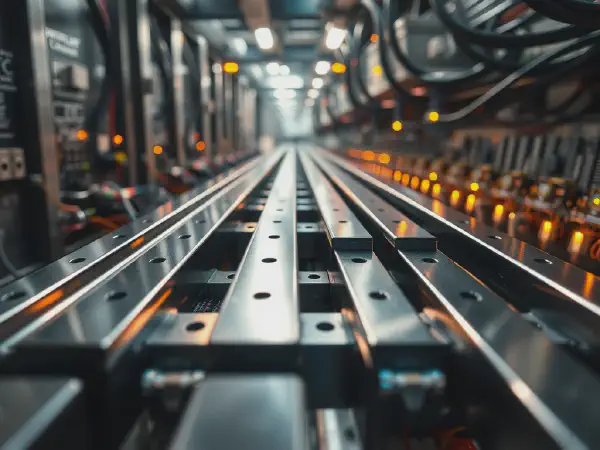
Understanding Aluminum Busbars: Properties, Applications, and Advantages
Aluminum busbars are essential components in electrical distribution systems, acting as conduits for electrical current in a wide range of applications. These bars are typically used to connect multiple circuits, enabling efficient power distribution and management. Aluminum, with its excellent conductivity and lightweight properties, serves as a practical alternative to copper for busbars, making them a popular choice in various industries.
One of the primary reasons aluminum busbars are favored is their remarkable electrical conductivity, which is approximately 60% that of copper. This means that while they may require a larger cross-sectional area compared to copper busbars to carry the same current load, they provide significant advantages in terms of weight and cost-effectiveness. Additionally, aluminum busbars exhibit excellent thermal conductivity, ensuring effective heat dissipation during operation.
Aluminum busbars are manufactured through several processes, including casting, extrusion, and forging. These processes enhance the material properties, ensuring durability and reliability in various settings. Moreover, their lightweight nature allows for easier handling and installation, further contributing to their widespread use in residential, commercial, and industrial electrical systems.
For efficient electrical distribution in industrial settings, the use of aluminum busbars offers superior performance and reliability.
The application of aluminum busbars spans multiple sectors, including residential electrical networks, industrial machinery, and renewable energy systems. In residential settings, aluminum busbars simplify the organization of electrical panels, while in industrial applications, they facilitate the distribution of power to heavy machinery. Furthermore, the role of aluminum busbars in renewable energy systems, such as solar and wind energy, underscores their significance in modern electrical infrastructure.
Overall, aluminum busbars are integral to efficient electrical distribution, offering a balance of performance, safety, and cost savings. Their versatility across applications makes them a preferred choice among engineers and electricians worldwide.
Manufacturing Processes of Aluminum Busbars
The manufacturing of aluminum busbars involves several methods to achieve desired specifications and properties. The casting process is one of the traditional methods where molten aluminum is poured into molds to form the desired shape of the busbar. This method allows for intricate designs and quick mass production, making it suitable for large-scale applications.
Extrusion is another common technique used in manufacturing aluminum busbars. In this process, aluminum billets are heated and forced through a die to create long rods or profiles with uniform cross-sections. This technique is particularly effective for producing lightweight and strong busbars, as well as offering additional benefits such as enhanced surface finishes and tailored dimensions.
Die forging is also employed in producing aluminum busbars, where heated aluminum is mechanically pressed into desired shapes using a die. This method enhances the material's strength and durability, making it suitable for environments where high mechanical loads are present. The forging process provides tighter tolerances and superior surface integrity, crucial for electrical applications.
Applications of Aluminum Busbars
In residential electrical systems, aluminum busbars are integral for connecting circuit breakers and distributing electricity to different parts of the home. They simplify electrical panel designs and help in organizing electrical connections efficiently. Additionally, their lightweight nature allows for easy installation, making them user-friendly for both homeowners and electricians.
In industrial settings, aluminum busbars are widely used to power heavy machinery and equipment. Their high conductivity and cost-effectiveness make them suitable for environments where large amounts of power need to be distributed efficiently. Industries such as manufacturing, mining, and data centers utilize aluminum busbars to facilitate reliable power distribution and enhance operational efficiency.
Moreover, aluminum busbars play a crucial role in renewable energy systems, such as solar photovoltaic installations and wind turbine technologies. They effectively connect solar panels, inverters, and energy storage systems, while also ensuring minimal energy loss during distribution. Their applications in these sectors are vital for the transition towards sustainable energy solutions.
Advantages of Aluminum Busbars
One of the most significant advantages of aluminum busbars is their cost-effectiveness compared to copper busbars. Aluminum is generally less expensive than copper, making it a more economical choice for large-scale installations without sacrificing performance. This cost benefit is particularly attractive for budget-conscious projects needing reliable electrical infrastructure.
Additionally, aluminum busbars offer weight reduction benefits. Their lightweight nature simplifies transport and installation, reducing labor costs and time. This lightweight characteristic is especially advantageous in applications where structural load limitations are a concern, such as in overhead systems and mounted installations.
Corrosion resistance is another notable advantage of aluminum busbars. Aluminum naturally forms a protective oxide layer, preventing corrosion and enhancing its lifespan in various environments. This property ensures that aluminum busbars maintain optimal performance and reliability, especially in outdoor or harsh conditions where exposure to moisture and pollutants is common.
Design Considerations for Aluminum Busbars
When designing aluminum busbars, proper sizing and rating are critical to ensure safety and performance standards are met. It is important to calculate current-carrying capacity accurately based on factors such as ambient temperature, installation conditions, and desired safety margins. Oversizing may result in unnecessary costs, whereas undersizing could lead to overheating and failure.
Thermal management is another vital consideration in aluminum busbar design. Busbars may generate heat during operation due to electrical resistance, and ensuring adequate cooling through proper spacing, ventilation, and possibly heat sinks can prolong the lifespan and effectiveness of the busbars. Taking thermal properties into account helps prevent thermal runaway situations, ensuring safe operation.
Lastly, insulation and mounting options for aluminum busbars play a crucial role in their design. Selecting appropriate insulation materials and securely mounting busbars to minimize vibration and mechanical stress are essential to maintain safety and reliability in operation. careful attention to these details helps prevent short circuits and other electrical hazards.
Maintenance of Aluminum Busbars
Routine inspections are a vital aspect of maintaining aluminum busbars to ensure their durability and reliability. Regular checks for signs of wear, corrosion, or overheating can help identify potential issues before they escalate into significant problems. These inspections allow for timely remediation actions, ensuring the longevity of the electrical system.
Cleaning and maintenance best practices should also be observed for aluminum busbars. Dust, dirt, and debris can accumulate on busbars over time, hindering their performance. Establishing a regular cleaning schedule using appropriate non-corrosive cleaning agents can maintain optimal conductivity and prevent corrosion, supporting efficient power distribution.
Lastly, it’s essential to recognize signs of wear and how to address them promptly. Common indicators may include discoloration, signs of corrosion, and performance fluctuations. Addressing these issues by repairing or replacing damaged sections of the busbar ensures continued system reliability and safety, preventing unexpected downtime or hazards.